Together against Covid-19
Cross-departmental aid project
2020/04/04
The Departments of Architecture and Mechanical Engineering of the TU Darmstadt support Darmstadt clinics with additive manufactured full face masks.
The burden on the health care system due to the worldwide, very dynamic spread of Covid-19 is extremely high and the risk to the health of the population in Germany is currently estimated by the Robert Koch Institute to be high overall and very high for risk groups. Due to the further increase in the number of cases of infection and the increased stockpiling of medical protective equipment, the need for infection protection material is particularly high among medical institutions. For this reason, the Hessian Ministry of Economics called on Friday (March 27, 2020) for companies to support the procurement or manufacture of infection protection equipment.
In response, Mr. Peter Maier (Head of Model Construction Workshop, Architecture Department) and Mr. Mirko Feick (Head of Mechanical Workshop PTW | PtU, Mechanical Engineering Department) took the initiative to produce reusable full face masks at short notice. For this aid project, 300 metres of plastic film for the production of 900 face masks were provided free of charge by Paul Auer GmbH from Mannheim (plant engineering for sandblasting technology).
The use of 3D printing technology plays an essential role in the production of the plastic holder for attaching the face visors of the three-part full face mask. For this purpose, the technical infrastructure is provided by the model-making workshop of the Department of Architecture (ten 3D printers) as well as by the institutes of the Department of Mechanical Engineering pmd (four 3D printers), PTW and PtU (with one 3D printer each) (cf. Fig. 1). Both a clever geometric revision of the plastic holder by Mr. Peter Maier and the process-technological know-how of the two Darmstadt mechanical engineering PhD students Johannes Geis (Institute pmd, FB 16) and Holger Merschroth (Institute PTW, FB 16) made it possible to improve the originally two-part plastic holder from a production technology point of view. As a result, the headgear can now be produced in one piece, thus saving assembly steps, reducing the construction time by 25 % and achieving a significant increase in productivity.
The 16 3D printers currently in use produce 50 reusable full face masks per day. After a very short start-up time, the first 50 full face masks were distributed to the AGAPLESION ELISABETHENSTIFT and other clinics in the vicinity yesterday already (April 2, 2020).
All participating institutes and persons are happy about the opportunity to make such a valuable and solidary contribution in currently difficult times.
Text: Dr.-Ing. Thomas Heep, PTW / April 3, 2020
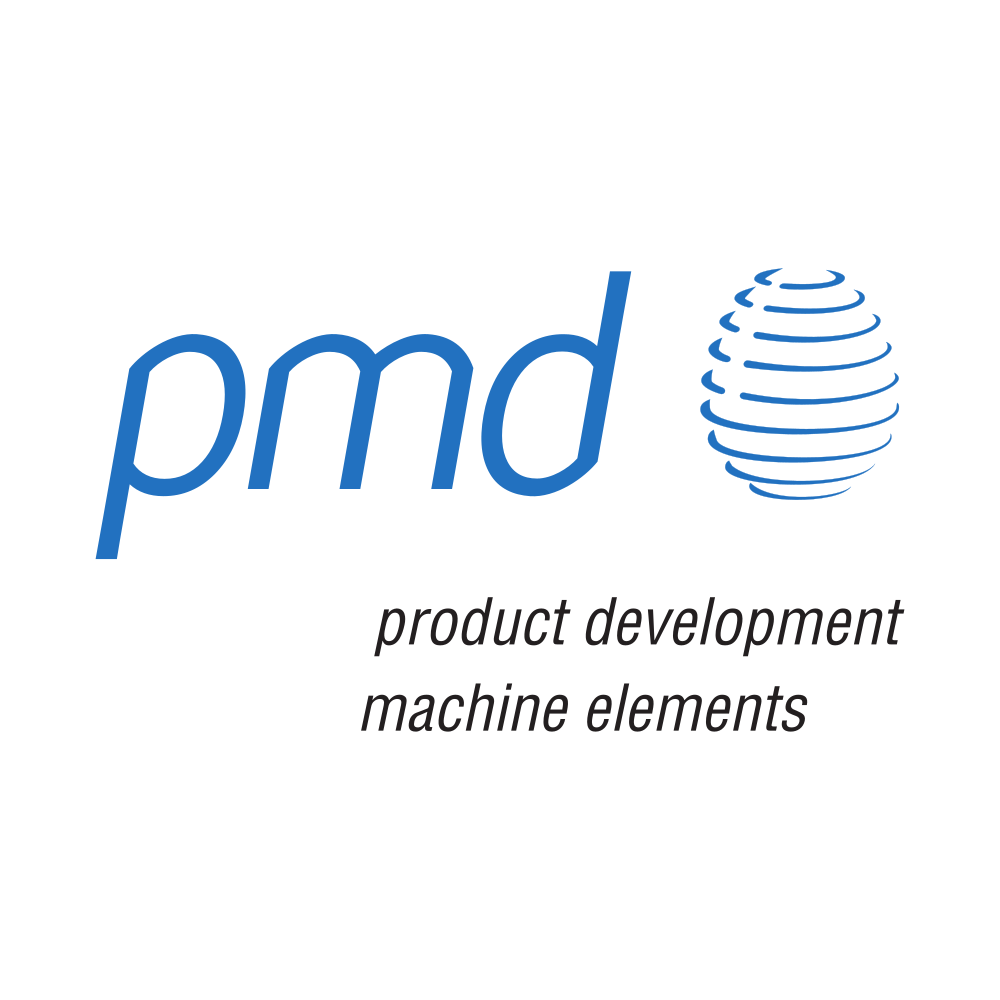