DataBelt
Components and methods for in-situ monitoring of high-performance timing belts
In this cooperative project, the department of Integrierte Elektronische Systeme (IES), BRECO Antriebstechnik Breher GmbH & Co. KG und der CONTECS Engineering Services GmbH worked together, to develop a sensing timing belt that can be used to determine the current state of wear and operating conditions. The project was funded by ZIM (Zentrales Innovationsprogramm Mittelstand) from the AiF (Arbeitsgemeinschaft industrieller Forschungsvereinigungen) under the funding code ZF 40126527.
Motivation
High-performance polyurethane timing belts are used in a wide range of industrial equipment for motionless transmission. The tension members, which are composed of steel cords, are enclosed in a polyurethane matrix that forms the teeth, cf. figure 1.
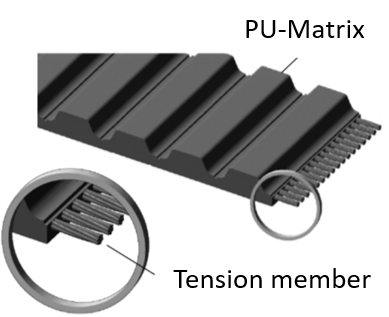
In the operation of industrial plants, the monitoring of plant and component status is increasingly being implemented as part of Industry 4.0. This can reduce maintenance costs and unplanned machine failures. Up to now, there has been no service life model for timing belts, which can lead to overdimensioning or unplanned machine failures. To determine the wear condition, maintenance personnel have so far measured the natural frequency in order to calculate the pretensioning force. Therefore, there is a high demand for measuring the wear and recording the operating conditions during operation.
Figure 2 shows the effect chain from the wear of the tension members to the measurement of the acceleration. With the measured acceleration, the natural frequency is to be detected in the frequency range in order to calculate the span force and finally the pretension force. With this procedure, the wear of the tension members can be determined.
Goal
Development of a sensing timing belt with which the temperature and acceleration in operation can be measured in all span segments. With this data, information about the operating condition as well as the wear condition is to be obtained via suitable data processing algorithms.
Results
In cooperation with the project partners, a sensor module was integrated into the tooth of a toothed belt. The main components are the acceleration and temperature sensor and the microcontroller with integrated Bluetooth data transmission. These components are integrated into a tooth with a sensor board, see figure 3. The high accelerations that occur during operation can damage the electronic components. Therefore, the sensor board was specifically reinforced to protect the main components [1].
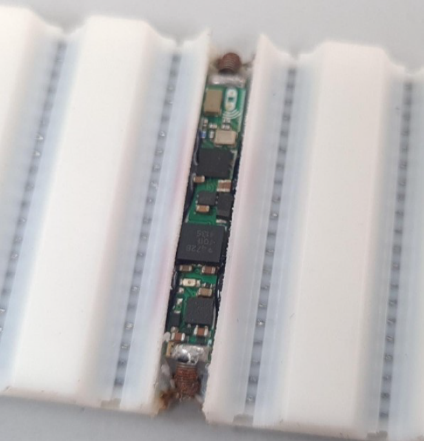
It was shown that the acceleration in the span segments can be measured and the change in the span force can be detected with the sensing timing belt. The measurement data is transferred into the frequency range by means of FFT to detect the natural frequency. The natural frequency can be reliably determined at low speeds by means of an analytical evaluation. At high speeds, overlaps with the tooth meshing frequency and interference frequencies can occur due to a partial exceeding of the measuring range of the acceleration sensor. To control these interferences, evaluation algorithms are to be developed in the future. [3]
[1] Großkurth, D., Martin, G., 2019. Intelligenter Zahnriemen, in 20. GMA/ITG-Fachtagung Sensoren und Messsysteme 2019, p. 738
[2] T. Nagel, Zahnriemengetriebe: Eigenschaften, Normung, Berechnung, Gestaltung. München: Hanser, 2008
[3] Koch Y., Weller R., Welzbacher, P., Kirchner E., 2022. In-Situ Condition Monitoring in Timing Belts for Automation Purposes – Challenges and Opportunities, in 32nd CIRP Design Conference