About the Research Area
The eTribosystems division investigates the electrical properties of rolling and plain bearings. By integrating rolling bearings into electrical circuits during operation, novel phenomena can be observed. One focus is the investigation of damaging effect of bearing currents. The spread of electric drives is also increasing in the course of the electrification of mobility, where damaging bearing currents occur in inverter-fed electric motors and lead to a bearing failure in the shortest possible time. If the electrical currents remain below a damaging effect, rolling and plain bearings can be used sensorial by measuring their electrical impedance to describe bearing forces or lubricant properties. To investigate these research fields, the department relies on experiments on the Athene rolling bearing test bench and other test facilities as well as on methods of numerical simulation and analytical modelling of the observed phenomena.
Furthermore, the limits of existing product development methods are analyzed and their enhancement for their application in mechanical and mechatronic engineering is examined.
Experiment
Current projects are investigating the electrical impedance of rolling and plain bearings under defined operating conditions and are comparing it with existing models in order to improve those and extend their operating limits. In addition, defined damaging currents are applied to bearings in order to develop a future damage model.
„Athene“ Test bench
In the Athene test bench, oil and grease lubricated bearings can be loaded axially and radially at defined speeds in four test chambers. These variables are controlled and measured. In addition, defined electrical currents can be conducted via the rolling bearings. Thus, rolling bearings can be tested under electrical and mechanical stress.
Technical Data | Measurement variables |
---|---|
4 Test chambers | Vibrations |
Axial loads up to 40 kN per bearing | Voltage and current measurement |
Radial loads up to 40 kN per bearing | Rotation speed |
Rotation speed up to 8000 min-1 | Temperature |
Temperature up to 90 °C | Axial and radial load |
Voltage- and current-controlled |
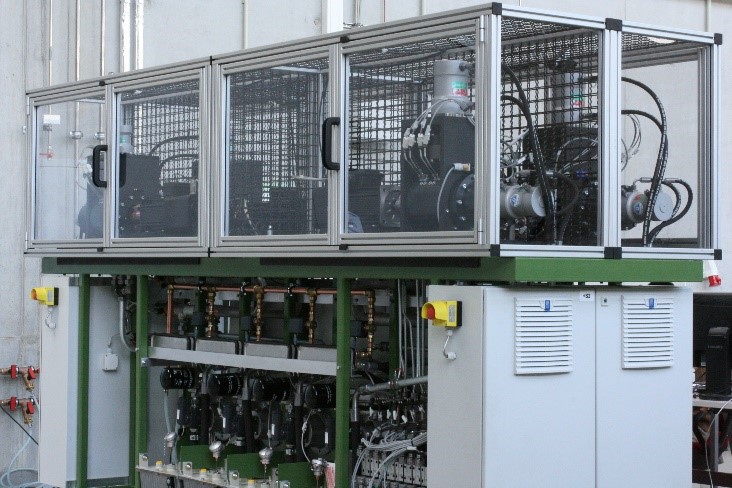

Simulation
In order to understand the mechanisms in electrically loaded and sensory used rolling bearings and to improve existing models for the description of these mechanisms, rolling bearing contacts are simulated using numerical methods. The core of this simulation task is the combination of numerical methods for flow simulation with finite element methods for solid state simulation to map the interactions of rolling elements, raceways and lubricants.