Imagine if we could look into the heart of your technical system!
In order to acquire specific process-related data and to generate new knowledge from it, the research area stands nationally and internationally for the research, development, integration and testing of sensing machine elements as well as the (digital) tools required for this.
Technical systems are oftentimes information processing systems – from classical mechatronic systems to networking cyber-physical systems of Industry 4.0 and Internet of Things (IoT). The functionality of these systems implies comprehensive information about machines or processes, which is recorded via a suitable sensing technology. For practical reasons, e.g. due to limitations regarding the available installation space, the protection of the sensor from the influence of acting disturbances or also the prevention of disturbances on the process from the integrated sensor itself, the variables of interest are often not measured directly at the “place of action” in an in-situ location. Instead, the variables of interest are oftentimes determined by means of a model from another, measured variable in an ex-situ location. The accuracy and quality of the information obtained thus depend on the quality of the utilized model and the assumptions made therein. Special attention is on the “distance” between the measured variables and the actual variables of interest. In addition to the spatial separation of the measurement location and the “place of action”, this also describes the increasingly complex model descriptions of the transmission path as well as the increasing influence of disturbances on the acquisition of measurement data.
The fundamental idea of Sensing Machine Elements (SME) is to reduce this uncertainty by integrating sensory, information-conducting as well as information-processing functions into machine and construction elements (β → 0). Machine elements are common and often standardized components of mechatronic systems in many applications and therefore offer the potential for a uniform integration of sensing technology. In addition, they are integral, function-fulfilling components of mechatronic systems. For example, they connect two subsystems of a mechatronic system. By integrating sensory functions into this interface, the behaviour of the system can be monitored more directly than it would be possible with external sensing technology. Due to the proximity of the sensor to the process, the corresponding model used for the interpretation of the sensor signal is much simpler than the one used in a process-distinct measurement. In addition, the required sensing technology outside the mechanical path of the system can be reduced.
Fields of application
Examples for possible fields of application of SME are:
- Integration of sensing technology with minor adaptions in design by replacing conventional machine elements with SME.
- Determination of load spectra for component design as part of product development
- Monitoring of manufacturing processes
- Condition monitoring and predictive maintenance
Application examples
Examples of (prototypically) implemented applications of SME:
- Measurement of the bearing load and identification of bearing damage by evaluating the electrical impedance of a rolling or plain bearing
- Temperature or force measuring screw
- Measurement of the trum forces of a timing belt by integrating acceleration and temperature sensors
- Measurement of shaft offset as well as the transmitted torque of compensating couplings
- Measurement of relevant variables directly on the construction element involved in the process
- Measurement of instantaneous angular speed of gears with magnetoresistive sensors to predict the state of damage
Research approach
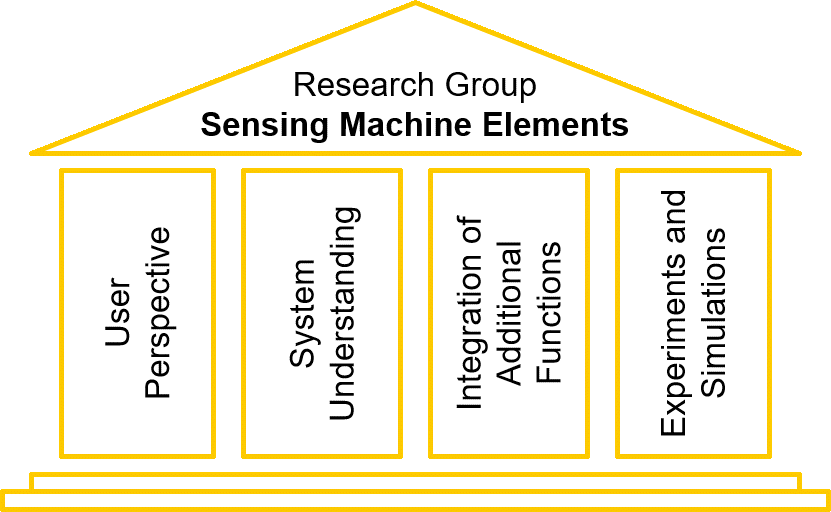
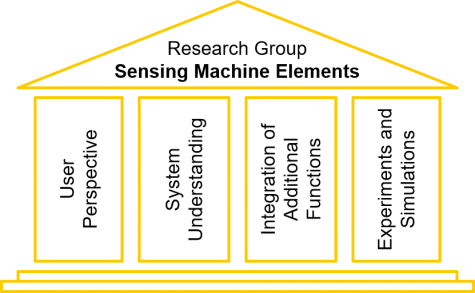
The research approach of the AB SME considers four fields:
From the user perspective, the key research question is what information adds value to the business and therefore the costumer and how can information be acquired in a robust way through measurement and data processing.
To enable a predictable and reliable function integration, a comprehensive system understanding of both mechanical and electric behaviour and the underlying properties of the machine element itself is required.
Development of innovative possibilities for the design integration of the additional functions into conventional machine elements as well as other construction elements.
Experimental investigations as well as numeric simulations are utilized to improve the mechatronic understanding of components and systems and to validate theoretical research results.
Recent research projects
Funded by the German Research Association (Deutsche Forschungsgesellschaft, DFG):
- Derivation of analysis- and synthesis-methods to manage uncertainty in the development of mechatronic systems with sensor integrating machine elements (Project number: 426030644, processed by Peter Welzbacher, M. Sc.)
- Product development with sensor integrating machine elements – Managing uncertainty associated to in-situ acquired sensor data in mechatronic systems (Project number: 431606807, processed by Maximilian Hausmann, M. Sc.)
- Microelectronic modular system for sensor-integrated machine elements (Project number: 466493340, processed by Richard Breimann, M. Sc.)
Funded by the European Regional Development Fund (Europäischer Fonds für regionale Entwicklung, EFRE):
- Establishment of a validation infrastructure for condition monitoring of large gearboxes in industrial applications with focus on sensor integration into gearboxes (Processed by Yanik Koch, M. Sc.)
Funded by the Landes-Offensive zur Entwicklung Wissenschaftlich-ökonomischer Exzellenz (LOEWE):
- Development of an intelligent emergency shut-off valve for liquid gas tanks (HA-Project number: 799/19-119 of LOEWE funding line 3 of the Hessenagentur, processed by Benjamin Kraus, M. Sc. M. Eng.)
Lectures & Courses
The development and application of conventional and innovative machine elements is subject of the basic lecture “Machine Elements and Mechatronics II” and especially in the advanced lecture “Innovative Machine Elements”.
Industrial cooperation projects
We strive for intensive cooperation with partners from industry in order to apply and improve our research results in industrial development and research projects. Just contact us if you are interested!
Employees of the research group
Doctoral theses
- Schork, S. (2020) ‚Methodische Entwicklung aussagekräftiger Prototypen durch Analyse der Produktkonfiguration‘, Technical University of Darmstadt.
- Vogel, S. (2021) ‚Das Lastpfad und Knotenmodell – Eine Erweiterung des C&C²-Ansatzes zur Bewertung von Ersatzgrößen in der Produktentwicklung mechatronischer Systeme‘, Technical University of Darmstadt.
- Vorwerk-Handing, G. (2021) ‚Erfassung systemspezifischer Zustandsgrößen – Physikalische Effektkataloge zur systematischen Identifikation potentieller Messgrößen‘, Technical University of Darmstadt.
- Martin, G. (2021) ‚Die Wälzlagerimpedanz als Werkzeug zur Untersuchung von Oberflächenabweichungen in Wälzlagern‘, Technical University of Darmstadt.